As we will discuss in this article, cobots can add tremendous value to your operations, but you should be sure to pay attention to risk assessments and safeguarding requirements.
Strategies for ensuring operator safety in the collaborative workspace
The collaborative robot (cobot) market is constantly growing as manufacturers search for solutions with more advanced technologies that can help overcome evolving internal and external pressures. These pressures include labor shortages, improving overall equipment effectiveness (OEE), customization, and job satisfaction improvement.
Cobots are one of the most popular robotic applications that help manufacturers fill gaps in automation and improve production. They offer several trending solutions, such as higher payloads that provide flexibility in handling complex production requests, mobile manipulators for material handling, compact solutions with a smaller footprint and safety features, and production management with Edge computing and artificial intelligence (AI) to improve machine efficiency and anticipate failures.
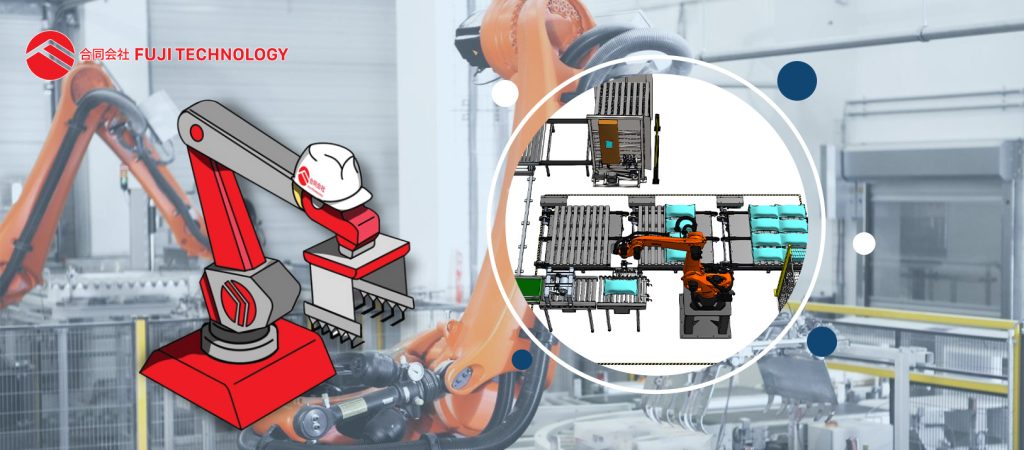
As we will discuss in this article, cobots can add tremendous value to your operations, but you should be sure to pay attention to risk assessments and safeguarding requirements.
Integrating, programming, and connecting the cobots to the rest of the plant
When determining how to make a collaborative robot add value within a wider automated system, manufacturers should complete the following steps:
- Establish goals
- Identify areas of human interaction or isolated robot work
- Find a risk assessor to assess the collaborative workspace
- Ensure that the cobot’s safety circuit is integrated into the larger system/solution
Collaborative robots provide different network communication options that allow them to be integrated with machine controllers, PLCs, or industrial PCs. Through the network, an operator can access a cobot’s parameters to exchange data. This makes it possible to access to the position, speed, and torque information from PLC and also send commands to the cobot from an external controller.
Easy programming is one of the great benefits of working with cobots. The programming language is significantly more intuitive compared to the traditional robots, which dramatically reduces the development time of the project. The programming is done in a flow chart, and we can access the software through the robot controller, pendant, or an external computer.
Which safety features are important for choosing a cobot?
In general, a cobot needs to have a mechanical structure capable to avoid crush points during its movement. Also, it should have safety sensors and circuits capable of identifying any type of collision in all its joints. Typically, the cobot has an external controller where it is possible to integrate other components using the safety inputs and outputs. It is important to analyze the safety category that each circuit and operation mode reaches to ensure that the cobot will meet the requirements of the safety project.
The cobot needs to offer a sufficient number of safety I/Os, safety zones, inputs to change the operation mode of the cobot, and indicators to show which mode the cobot is currently functioning in. Additionally, the cobot needs to have features to be easy to use and quickly re-configurable in case of changes in the manufacturing process. In terms of tools and accessories, some applications require a safety sensor in the gripper, which means that the gripper should be capable to identify the opening/closing position to avoid squeezing of operators’ hands and fingers. Additional forcing sensors can also be integrated to identify collision in the tool, especially in applications of machine tending where the cobot is responsible to fit parts in the machine tool.
Summary
Collaborative robots can be a game-changing investment for many companies, and they do contain design elements that make them much less dangerous than traditional industrial robots. That said, safety measures are still very important to protect any operator who must enter the collaborative workspace. A thorough machine safety risk assessment will help you determine the cobot’s safety category and implement the correct safety I/Os, safety zones, and indicators.
roboticstomorrow.com
Pingback: buying androxal generic europe
Pingback: how to buy enclomiphene cheap usa
Pingback: order rifaximin canada how to buy
Pingback: cheapest buy xifaxan generic online uk
Pingback: ordering staxyn generic cheap
Pingback: order avodart generic effectiveness
Pingback: how to buy dutasteride cheap store
Pingback: how to order flexeril cyclobenzaprine canada drugs
Pingback: online order gabapentin generic cheap
Pingback: buy cheap fildena australia suppliers
Pingback: cheapest buy itraconazole cheap online in the uk
Pingback: kamagra bez lékařského předpisu přes noc
Pingback: kamagra le numéro 800 pour passer commande