[PRODUCT NOTICE] PACKAGING ROBOT SYSTEM: MAXIMIZE THROUGHPUT AND PROFITS FOR THE INDUSTRY
Automated robots are increasingly being used by firms to pack finished goods into pallets. In order to replace workers at the labor-intensive, monotonous, and fraught with dangers stage of loading items. The robot’s 24/7 operation, which helps to steady output and assures high quality of final products for factories, especially increases the potential for production.
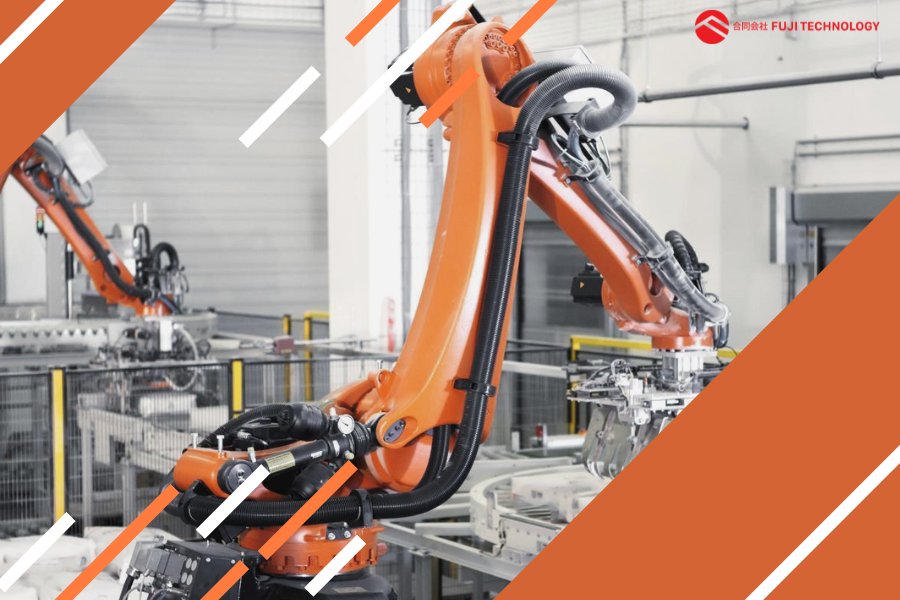
Packaging Robot in Industry
Our Packaging Robot System can perform many tasks, including opening, filling, transporting, palletizing, sealing, coding, and labeling product packaging. Almost any process involving the movement or packing of goods can be automated by a packaging robot. They can be applied in a wide range of industries (Food and beverage, Pharmaceuticals, Plastics, Building materials, …), they are commonly used in situations where products must be packaged consistently, accurately, and with high quality to ensure product integrity.
What kind of benefits do the packaging robot systems provide for manufacturers?
Comparing with manual processes, easy to find the outstanding advantage of packing robots. They provide speed, accuracy, and productivity, delivering a relatively quick return on investment (ROI) when deployed correctly.
So what exactly benefits do that Packaging robot system brings?
Increase product throughput
The packaging robot system is the most efficient method of resolving the bottleneck in manual production progress.
Most of our manufacturers who use this solution report a significant increase in throughput because there’s no need to concern with the speed of package, moving, and/or labeling products like before. The automation of these bottlenecks can have a significant impact on overall throughput with a stable frequency of up to 1000 times per hour and operating 24/7.
Fuji Technology always gives our customers expert advice to help them choose the right robot and end effector for application.
Reducing operation cost
In today’s hyper-competitive manufacturing environment, cost reductions are one of the most common reasons for automating. Manufacturers are looking for any way to cut costs. Packaging robots can perform more packaging tasks at a lower cost and with greater consistency than manual labor.
Reducing Occupational Accident
Many factories still use manual bag packing, which has several risks and limitations, including:
- The speed is not fast.
- Injury danger
- Limited cargo capacity
- Workplace time consistency is lacking.
- The pallet’s ability to synchronize is limited (goods are moved, unstable, …)
- High labor costs
When it comes to the loading and unloading process, these limitations have the most impact on businesses. If this is the case, it is time to consider automation is faster, stronger, more durable, and more reliable than manual operators, reduces bottlenecks, minimizes unnecessary damage, and increases operational efficiency.
Because of the nature of cargo handling applications, safety is the top priority for successful operations. Palletizing robots typically have a high load capacity and are fast.
This combination poses a risk to the operator, so appropriate safety and risk reduction devices should always be included when designing a system to help limit the possibility of injury in the workplace with the robot boots. This includes safety equipment (robot cages, safety sensors, and so on) to reduce the possibility of your robot injuring workers.
Do you still hesitate whether you’re ready for automated packaging? Our advisors are standing by to help you on your automation journey.